Accuracy Batch Polystyrene Pre-expander Machine
Product Overview
The Accuracy Batch Polystyrene Pre-expander Machine emerges as a paragon of energy-efficient innovation, purposefully engineered for the expansion of EPS polystyrene. This highly adaptable equipment serves as a comprehensive solution, addressing a broad spectrum of thermoplastic foam processing demands. It is equally well-suited for the expansive production lines of large-scale manufacturers and the more compact operations of smaller enterprises. With an unwavering commitment to minimizing material costs and maximizing energy savings, this machine consistently delivers outstanding performance and pinpoint precision in each and every batch it processes.
Main Features
- High-Quality Construction
The machine is furnished with a suite of top-tier components, commencing with a stainless steel dryer bed. Constructed from premium-grade stainless steel, it not only exhibits exceptional resistance to corrosion but also provides a stable and hygienic platform for the drying process. The screw conveyor, meticulously engineered with precisely calibrated helical flights and a variable speed drive, ensures a seamless and controlled transfer of material. The filling system, incorporating state-of-the-art valves and a highly accurate dosing mechanism, guarantees precise and consistent material introduction. Complemented by a sieving device equipped with adjustable meshes of the finest tolerances, the machine effectively filters out any impurities or irregularly sized particles, thereby safeguarding the integrity and quality of the final product. This ensemble of components not only endows the machine with long-lasting durability but also underpins its effective and efficient operation. - Precise Steam System
The machine's steam system is a marvel of engineering finesse. It features an accurate pressure reducer and a PID control system, which work in harmonious synergy to maintain a steam flow that is both stable and unerringly consistent. The pressure reducer, leveraging advanced valve technology, is capable of effectuating infinitesimal adjustments to the steam pressure, ensuring that it remains firmly within the optimal range. This meticulous control over steam pressure is of paramount importance, as it directly translates into uniform expansion of the EPS polystyrene. The result is a material of minimal variation in quality, meeting the most exacting standards of consistency and homogeneity. - Efficient Pressure Control
Integrated pressure sensors serve as the vigilant guardians of the expansion chamber's pressure stability. These highly sensitive sensors continuously monitor the internal pressure, promptly detecting any deviations and triggering corrective actions. Paired with a multi-steam exhausting system, which comprises multiple strategically positioned vents and valves, the machine is able to expel excess steam in a precisely calibrated manner. This not only helps to maintain a stable pressure environment but also significantly reduces steam consumption. By operating with such minimal waste, the machine maximizes energy efficiency, translating into both cost savings and a reduced environmental footprint. - Advanced Temperature Control
Equipped with a cutting-edge temperature sensor and a compressed air proportional valve, the machine exercises precise and unerring control over the expansion temperature. This level of control is particularly crucial for high-density expansion, where even the slightest temperature fluctuation can have a profound impact on the quality of the final product. By maintaining an accurate and stable temperature, the machine minimizes the occurrence of broken beads, ensuring a foam of more consistent quality. Moreover, the system is designed to optimize heat energy usage during the expansion process, conserving valuable resources and further enhancing the machine's overall energy efficiency. - Accurate Material Level Control
The styrofoam batch expander machine deploys a sophisticated material level control system, incorporating vibrating level sensors and highly accurate weighing scales. These components work in tandem to provide real-time monitoring of material levels. The vibrating level sensors, operating on the principle of vibration frequency modulation, accurately detect the height and density of the material. Paired with the weighing scales, which offer precise weight measurements, the system ensures minimal density tolerance. This translates into a consistent material flow and uniform expansion across all batches, eliminating variations and ensuring a product of unwavering quality. - Automated Material Filling System
The machine is equipped with a user-friendly touchscreen interface, which serves as the command center for material filling operations. Operators can effortlessly set the desired filling weight via this intuitive interface. The machine then automatically activates its electronic weighing system, which adjusts with remarkable precision to ensure accurate and consistent material filling for each batch. This automated process not only eliminates the potential for human error but also streamlines the production process, leading to significant improvements in production efficiency. - Reliable Electric Control
The PLC touch screen and electrical components, including valves, are sourced from globally renowned brands, renowned for their unwavering commitment to quality and reliability. This strategic choice ensures that the machine operates with stability and dependability. The PLC touch screen provides operators with a visual and interactive platform for monitoring and controlling the machine's functions. The electrical components, with their proven track record of performance, work in seamless harmony to automate the production process. This control system not only simplifies operation but also optimizes the entire production process, from start to finish.
Optional Features
- Auto Density-Weighing System: For those applications that demand the utmost level of accuracy, the machine offers an optional auto density-weighing system. This advanced technology provides real-time feedback and self-adjustment capabilities, ensuring that the foam density remains consistent throughout the expansion process. By continuously monitoring and adjusting the density, the system enables manufacturers to produce foam with customized density profiles, meeting the specific requirements of a wide range of applications, from high-performance insulation to intricate packaging designs.
- Secondary Expansion Device: The SPJ130 and SPJ160 models come with an optional secondary expansion device, which represents a significant enhancement to the machine's capabilities. This device enables a secondary stage of expansion, further refining the foam quality and expanding capacity. It is particularly valuable for applications that require enhanced insulation properties or lightweight foam products, providing manufacturers with the flexibility to meet the diverse and evolving demands of the market.
Key Benefits
- Energy-Efficient
The machine's advanced steam and temperature control systems are the cornerstones of its energy-efficient design. By precisely regulating steam usage and optimizing heat energy consumption, the machine achieves significant reductions in both steam and heat consumption. This not only translates into cost savings for manufacturers but also aligns with the growing global emphasis on sustainable manufacturing practices. - Reduced Material Costs
The precise pressure and material control systems embedded within the machine are instrumental in ensuring uniformity in the foam quality. By minimizing waste and maximizing the utilization of raw materials, the machine helps manufacturers to reduce material costs. This is achieved through accurate control over the expansion process, which ensures that each batch of foam is produced with the optimal density and consistency, eliminating the need for excessive material usage or rework. - Consistent Output
With its accurate weighing, pressure, and temperature control systems, the machine delivers a level of precision that is second to none. This results in consistent foam expansion, batch after batch, and a significant reduction in defective products. The machine's ability to maintain a stable and controlled production environment ensures that the final product meets the highest standards of quality and consistency, enhancing customer satisfaction and brand reputation. - Automation
The PLC touchscreen interface and automated filling system revolutionize the way operators interact with the machine. The touchscreen provides a simple and intuitive platform for monitoring and controlling all aspects of the machine's operation. The automated filling system eliminates the need for manual intervention, reducing the potential for human error and improving overall productivity. This automation not only streamlines the production process but also frees up operators to focus on other critical aspects of the manufacturing operation.
Conclusion
The Accuracy Batch Polystyrene Pre-expander Machine stands as a testament to high-performance, energy-efficient engineering. With its advanced control systems, precise material handling, and automated features, it offers a cost-effective and reliable solution for high-quality foam production.
If you are seeking to elevate your EPS production to new heights, with a machine that combines precision, efficiency, and reliability, the Accuracy Batch Polystyrene Pre-expander Machine is the quintessential choice. Contact us today to unlock a world of possibilities and gain access to more information or to request a quote.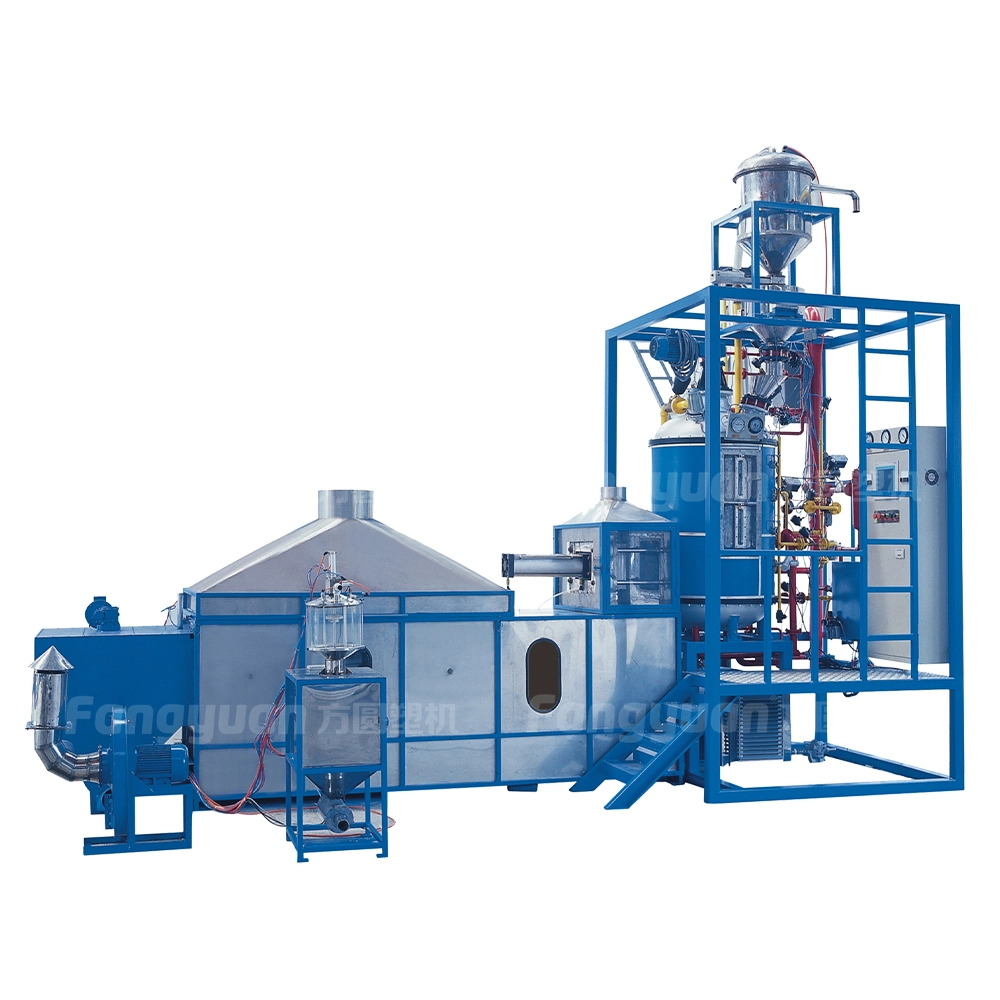
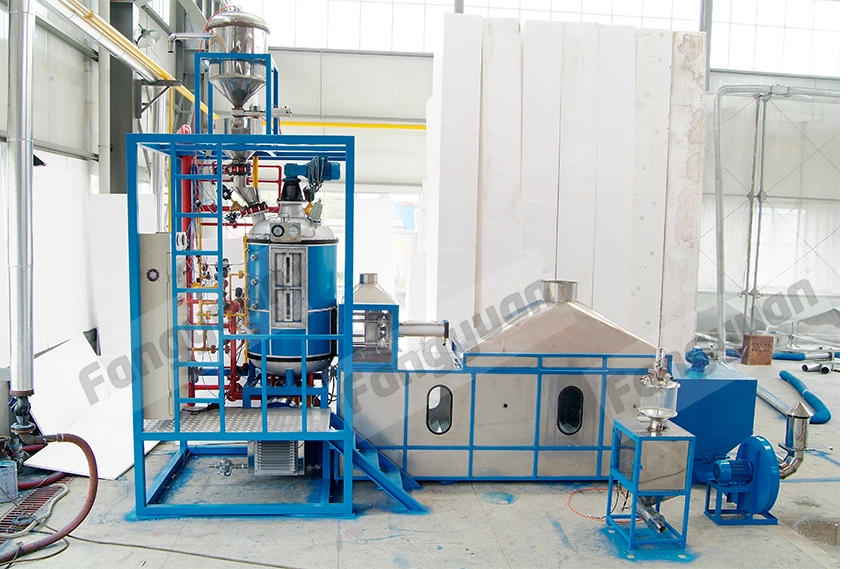
The machine is furnished with a suite of top-tier components, commencing with a stainless steel dryer bed. Constructed from premium-grade stainless steel, it not only exhibits exceptional resistance to corrosion but also provides a stable and hygienic platform for the drying process. The screw conveyor, meticulously engineered with precisely calibrated helical flights and a variable speed drive, ensures a seamless and controlled transfer of material. The filling system, incorporating state-of-the-art valves and a highly accurate dosing mechanism, guarantees precise and consistent material introduction. Complemented by a sieving device equipped with adjustable meshes of the finest tolerances, the machine effectively filters out any impurities or irregularly sized particles, thereby safeguarding the integrity and quality of the final product. This ensemble of components not only endows the machine with long-lasting durability but also underpins its effective and efficient operation.
The machine's steam system is a marvel of engineering finesse. It features an accurate pressure reducer and a PID control system, which work in harmonious synergy to maintain a steam flow that is both stable and unerringly consistent. The pressure reducer, leveraging advanced valve technology, is capable of effectuating infinitesimal adjustments to the steam pressure, ensuring that it remains firmly within the optimal range. This meticulous control over steam pressure is of paramount importance, as it directly translates into uniform expansion of the EPS polystyrene. The result is a material of minimal variation in quality, meeting the most exacting standards of consistency and homogeneity.
Integrated pressure sensors serve as the vigilant guardians of the expansion chamber's pressure stability. These highly sensitive sensors continuously monitor the internal pressure, promptly detecting any deviations and triggering corrective actions. Paired with a multi-steam exhausting system, which comprises multiple strategically positioned vents and valves, the machine is able to expel excess steam in a precisely calibrated manner. This not only helps to maintain a stable pressure environment but also significantly reduces steam consumption. By operating with such minimal waste, the machine maximizes energy efficiency, translating into both cost savings and a reduced environmental footprint.
Equipped with a cutting-edge temperature sensor and a compressed air proportional valve, the machine exercises precise and unerring control over the expansion temperature. This level of control is particularly crucial for high-density expansion, where even the slightest temperature fluctuation can have a profound impact on the quality of the final product. By maintaining an accurate and stable temperature, the machine minimizes the occurrence of broken beads, ensuring a foam of more consistent quality. Moreover, the system is designed to optimize heat energy usage during the expansion process, conserving valuable resources and further enhancing the machine's overall energy efficiency.
The styrofoam batch expander machine deploys a sophisticated material level control system, incorporating vibrating level sensors and highly accurate weighing scales. These components work in tandem to provide real-time monitoring of material levels. The vibrating level sensors, operating on the principle of vibration frequency modulation, accurately detect the height and density of the material. Paired with the weighing scales, which offer precise weight measurements, the system ensures minimal density tolerance. This translates into a consistent material flow and uniform expansion across all batches, eliminating variations and ensuring a product of unwavering quality.
The machine is equipped with a user-friendly touchscreen interface, which serves as the command center for material filling operations. Operators can effortlessly set the desired filling weight via this intuitive interface. The machine then automatically activates its electronic weighing system, which adjusts with remarkable precision to ensure accurate and consistent material filling for each batch. This automated process not only eliminates the potential for human error but also streamlines the production process, leading to significant improvements in production efficiency.
The PLC touch screen and electrical components, including valves, are sourced from globally renowned brands, renowned for their unwavering commitment to quality and reliability. This strategic choice ensures that the machine operates with stability and dependability. The PLC touch screen provides operators with a visual and interactive platform for monitoring and controlling the machine's functions. The electrical components, with their proven track record of performance, work in seamless harmony to automate the production process. This control system not only simplifies operation but also optimizes the entire production process, from start to finish.
The machine's advanced steam and temperature control systems are the cornerstones of its energy-efficient design. By precisely regulating steam usage and optimizing heat energy consumption, the machine achieves significant reductions in both steam and heat consumption. This not only translates into cost savings for manufacturers but also aligns with the growing global emphasis on sustainable manufacturing practices.
The precise pressure and material control systems embedded within the machine are instrumental in ensuring uniformity in the foam quality. By minimizing waste and maximizing the utilization of raw materials, the machine helps manufacturers to reduce material costs. This is achieved through accurate control over the expansion process, which ensures that each batch of foam is produced with the optimal density and consistency, eliminating the need for excessive material usage or rework.
With its accurate weighing, pressure, and temperature control systems, the machine delivers a level of precision that is second to none. This results in consistent foam expansion, batch after batch, and a significant reduction in defective products. The machine's ability to maintain a stable and controlled production environment ensures that the final product meets the highest standards of quality and consistency, enhancing customer satisfaction and brand reputation.
The PLC touchscreen interface and automated filling system revolutionize the way operators interact with the machine. The touchscreen provides a simple and intuitive platform for monitoring and controlling all aspects of the machine's operation. The automated filling system eliminates the need for manual intervention, reducing the potential for human error and improving overall productivity. This automation not only streamlines the production process but also frees up operators to focus on other critical aspects of the manufacturing operation.
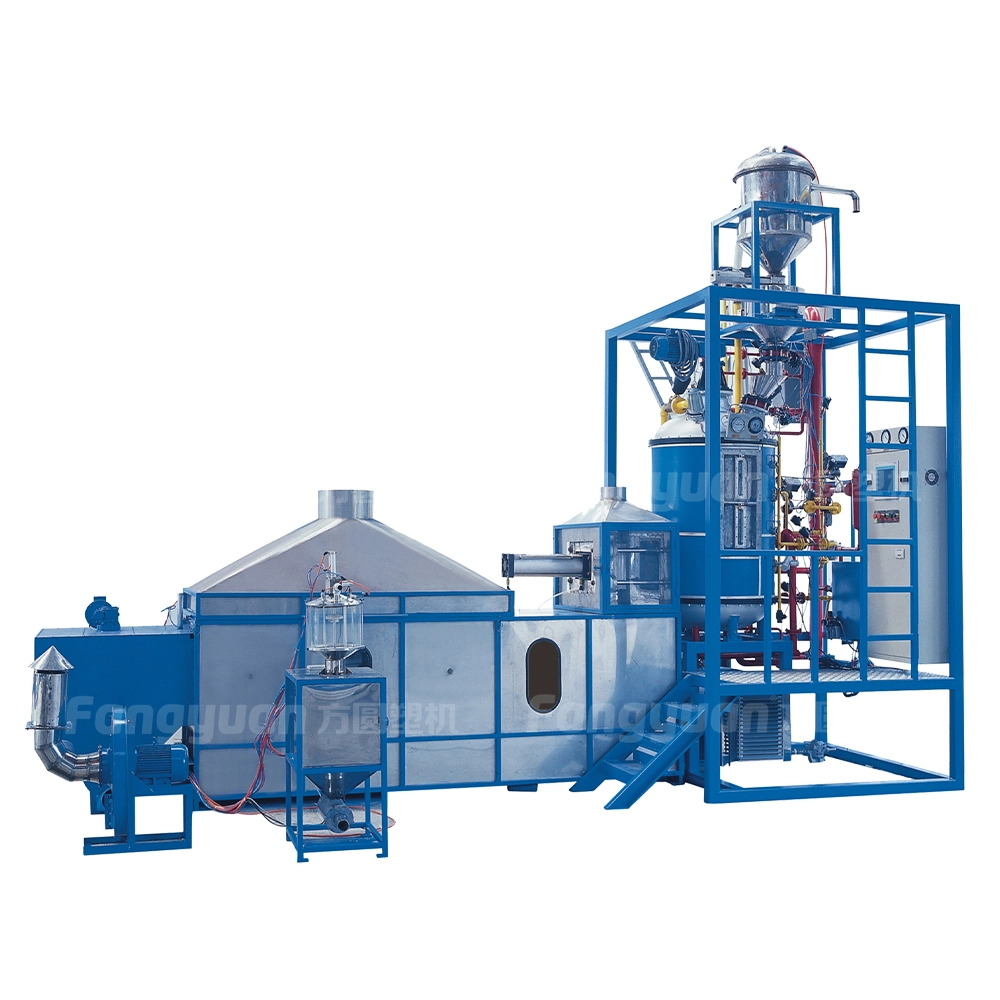
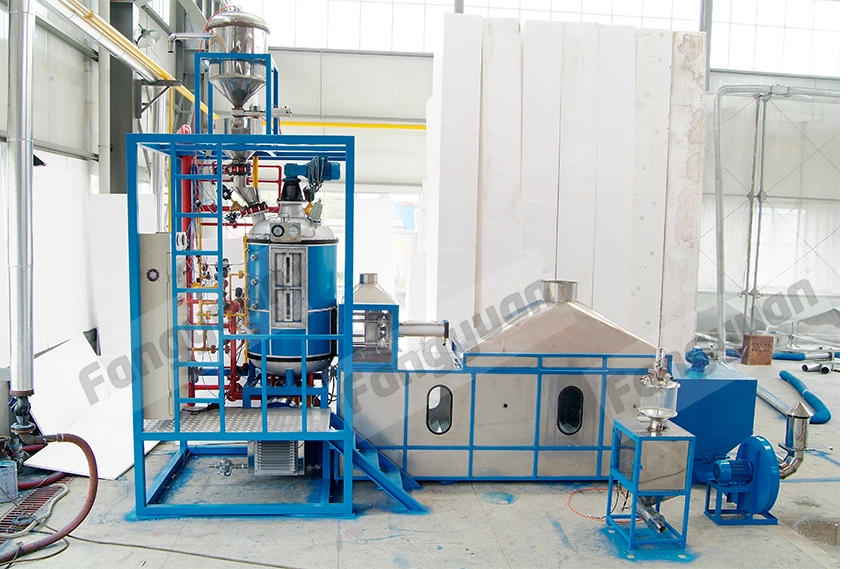